HALE UAV Technology
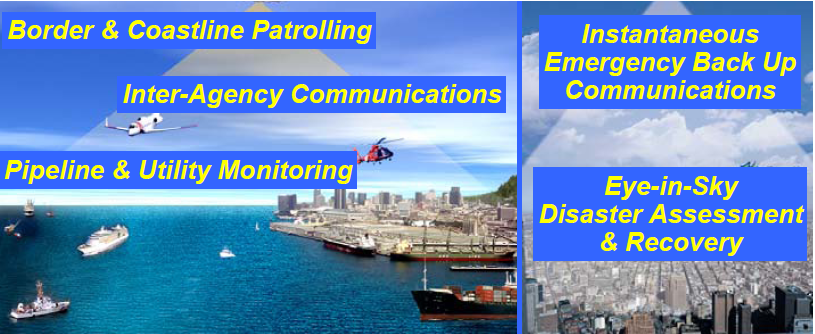
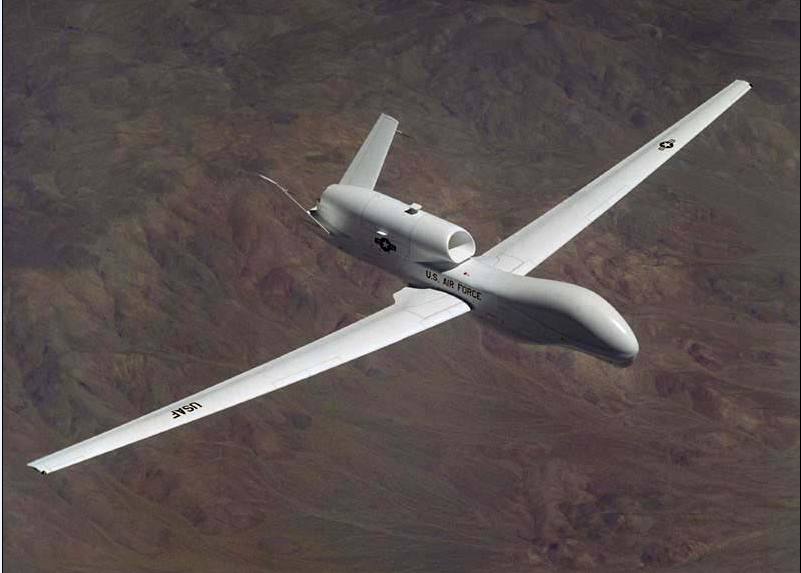
Maximum 48 Hours Endurance
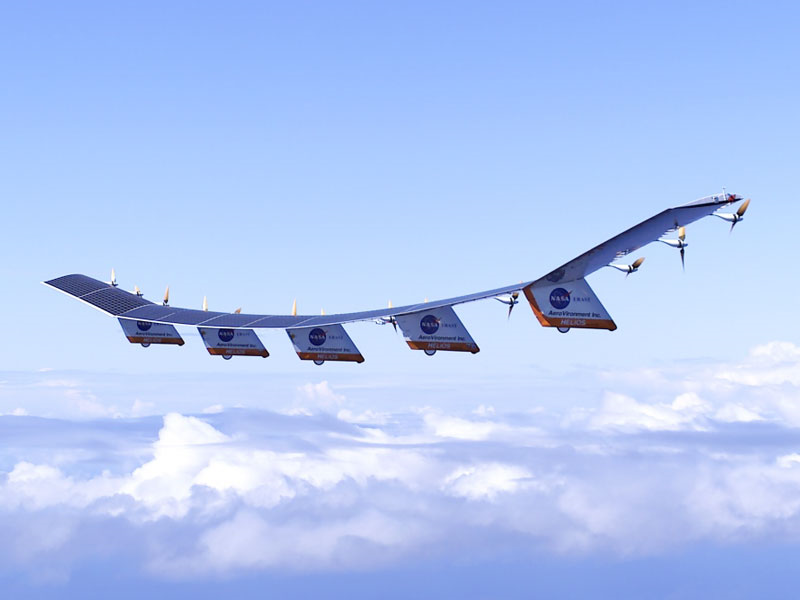
Potentially Unlimited Endurance
Cognitive UAV Mission Requirements
- Rapidly deployable, highly survivable ISR platform
- Ability to take-off from small general aviation runways (4000ft x 75ft)
- Loiter at 60,000 ft for 15 days with 99% probability of station keeping
- Payload is assumed to be 250 lbs and the power consumption is 1.5 kW – distributed among the cellular aircraft
Solar Cell / Rechargeable Battery Technology
Solar Cell | Type | Power Density (W/ft2) | Areal Density (lb/ft2) | Efficiency (%) |
Sunpower A300 | Thin Film Cell | 18.6 | 0.143 | 20 |
Emcore IMM | Thin Film Cell | 30.6 | > 0.1 | ~ 33 |
- Commercially available thin film solar cell efficiencies ~20%
- Will approach 30% in near future
Battery | Battery Chemistry | Max. Discharge (C) | Voltage (V) | Energy Density |
Sanyo UR18650F | Lithium-Ion | 2 | 3.7 | 191 W-h/kg |
Varta PLF 523450 | Lithium Polymer | 2 | 3.7 | 231 W-h/kg |
SION Power Cell | Lithium-Sulfur | 2 | 3.6 | 350 W-h/kg |
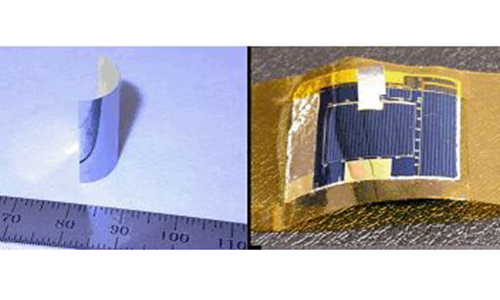
Emcore IMM-3J
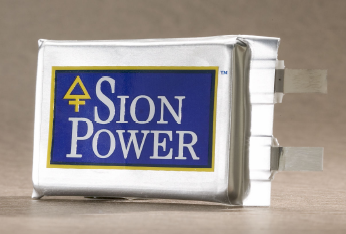
Lithium Sulfur Cell
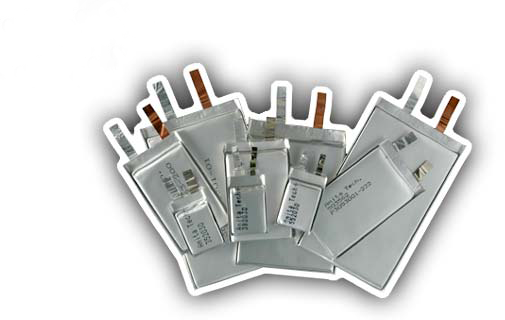
Lithium Polymer Cell
Conceptual Design Trade Study Conclusions
- Minimizing the drag is imperative and retracting or eliminating the landing gear has a significant impact on designs limited by battery energy density
- Select a power loading of 30 W/lbs as there is little difference in the impact of a power loading of either 20 or 30 W/lbs
- For the current battery technology 8 linked vehicles offer a significant increase in mission feasible days
Cellular UAV Conceptual Design
e | 0.8 |
CDo | 0.008 |
W/S | 1 psf |
(P/W)max | 30 W/lb |
AR (cellular) | 5 |
AR (docked) | 40 |
Wingspan (cellular) | 67 ft |
Wingspan (docked) | 536 ft |
W (cellular) | 900 lbs |
W (docked) | 7200 lbs |
Feasible Mission Days | 187 |
CLcruise | 1.17 |
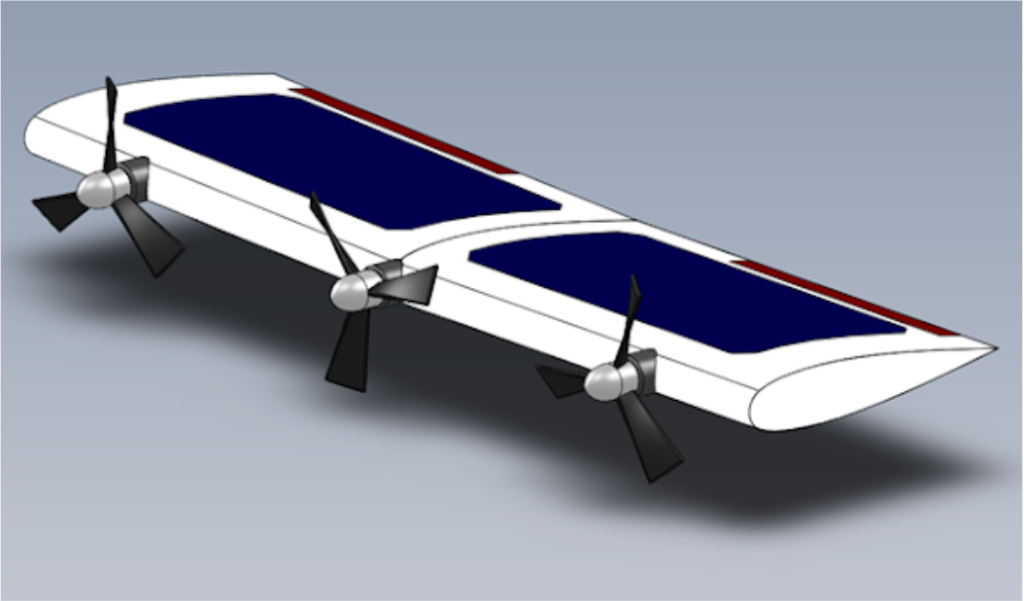
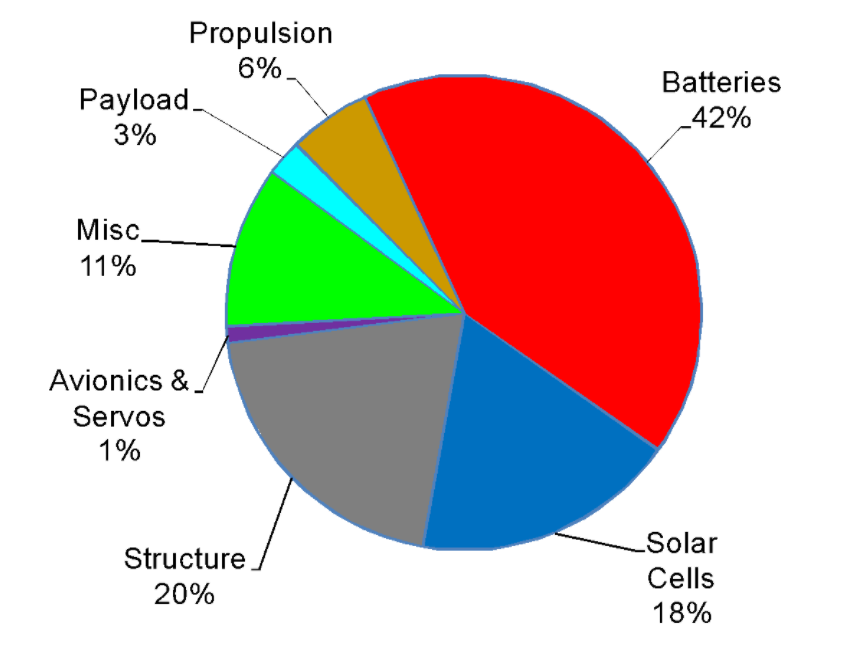
Cellular UAV Conceptual Design
- Developing in-house autopilot for docking demonstration using PC-104 stack
- Simulation of linked vehicle dynamics and control
- High level communication and control for vehicle coordination and threat avoidance
- Optimal trajectory determination for docking when taking close proximity aerodynamics into account
- Simulation of the Cognitive UAV mission in Flight Gear
Risk Mitigation Flight Testing
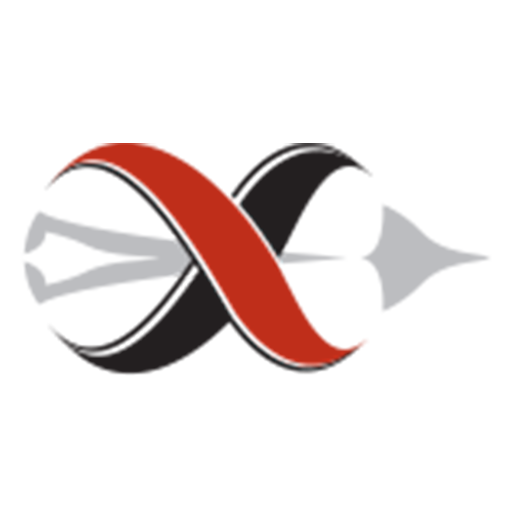
Evaluate the high risk technologies
- Demonstrate the integration of local proximity sensor technology in a flight environment
- Achieve autonomous close formation flight maneuvers with two vehicles
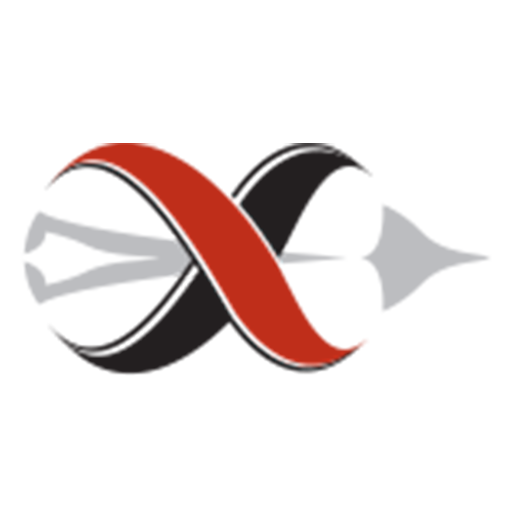
Reduced risk considerations
- Use proven commercial off-the-shelf components, including the vehicles and autopilot system
- The flight maneuvering, speed, and performance objectives are minimal.
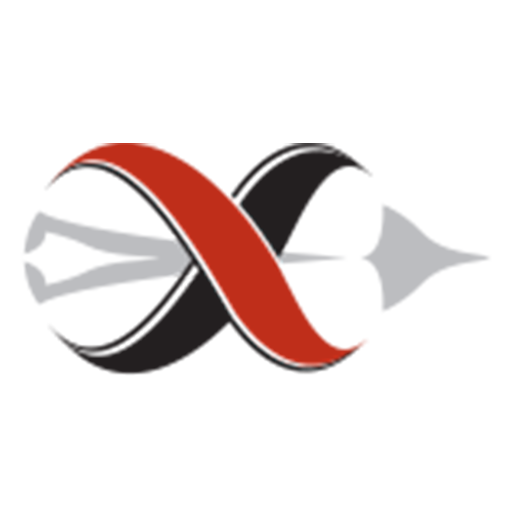
Desired outcome from flight tests
- Computer-controlled flight maneuvers with separations of less than one wingspan using onboard sensor augmentation.
Subscale Vehicle Design
- Based on the conceptual design, the preliminary design of the subscale cellular vehicle was made
- This vehicle will be fabricated in 2011 and flown in 2012.
Parameter | Value |
Aircraft Weight | 185 lbs |
Wing Span | 20 ft |
Wing Root Chord | 3.96 ft |
Wing Tip Chord | 3.96 ft |
AR | 6.19 |
Static Margin | 8 % |
L.E. Spar Diameter | 5 in |
T.E. Spar Diameter | 1.5 in |
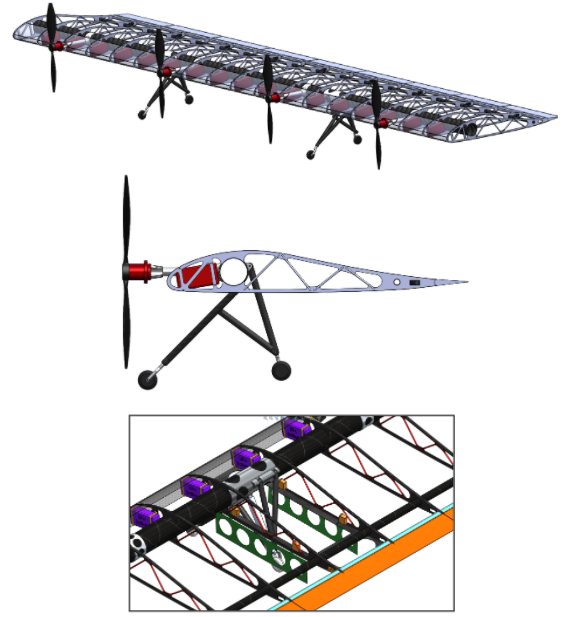
Docking Vehicle Design
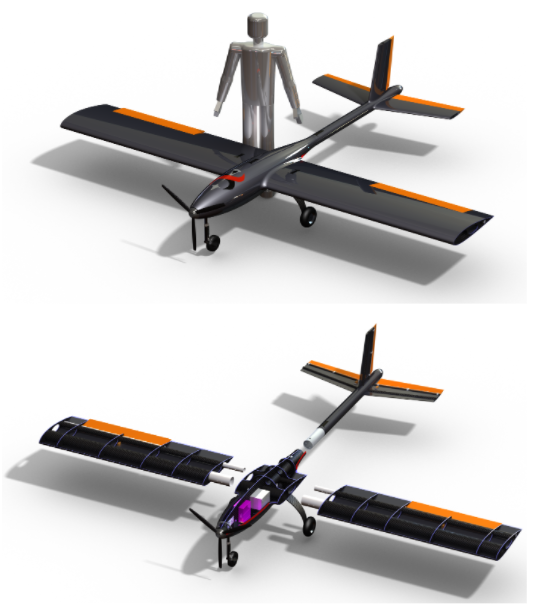
- A low cost custom vehicle is being designed and fabricated by NextGen to demonstrate in-flight tip-to-tip docking of UAVs
- This aircraft will be fabricated in 2010 and flight tested in 2010-2011
Parameter | Value |
Aircraft Weight | 120 lbs |
Wing Span | 13.5 ft |
Wing Root Chord | 2.2 ft |
Wing Tip Chord | 2.2ft |
AR | 6.19 |
Aircraft Length | 10.8 ft |
Aircraft Height | 3.6 ft |
Static Margin | 10 % |
L.E. Spar Diameter | 4 in |
T.E. Spar Diameter | 2 in |
Vehicle Docking Concept
- A ball and socket docking mechanism was selected bas on assessment of possible mechanisms
- A soft docking boom is extended from the aircraft wingtip during flight to the tip of the adjacent aircraft
- A hard dock is then performed at the leading and trailing edges as the soft docking boom retracts
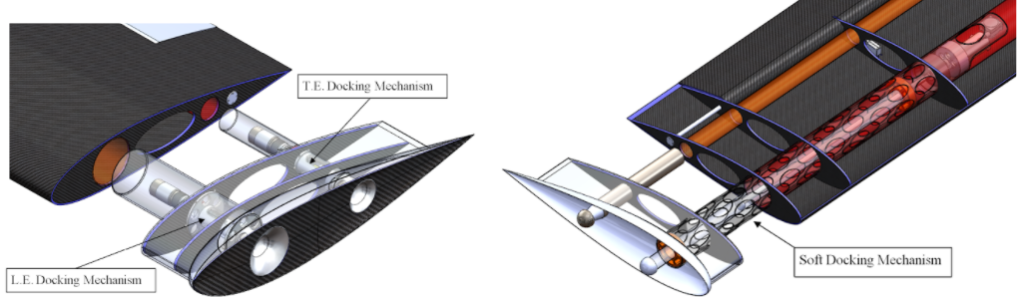
- Three docking mechanism prototypes have been designed and fabricated
- Their performance will be fully characterized with benchtop testing and the final selection will be made
Docking Mechanism Design
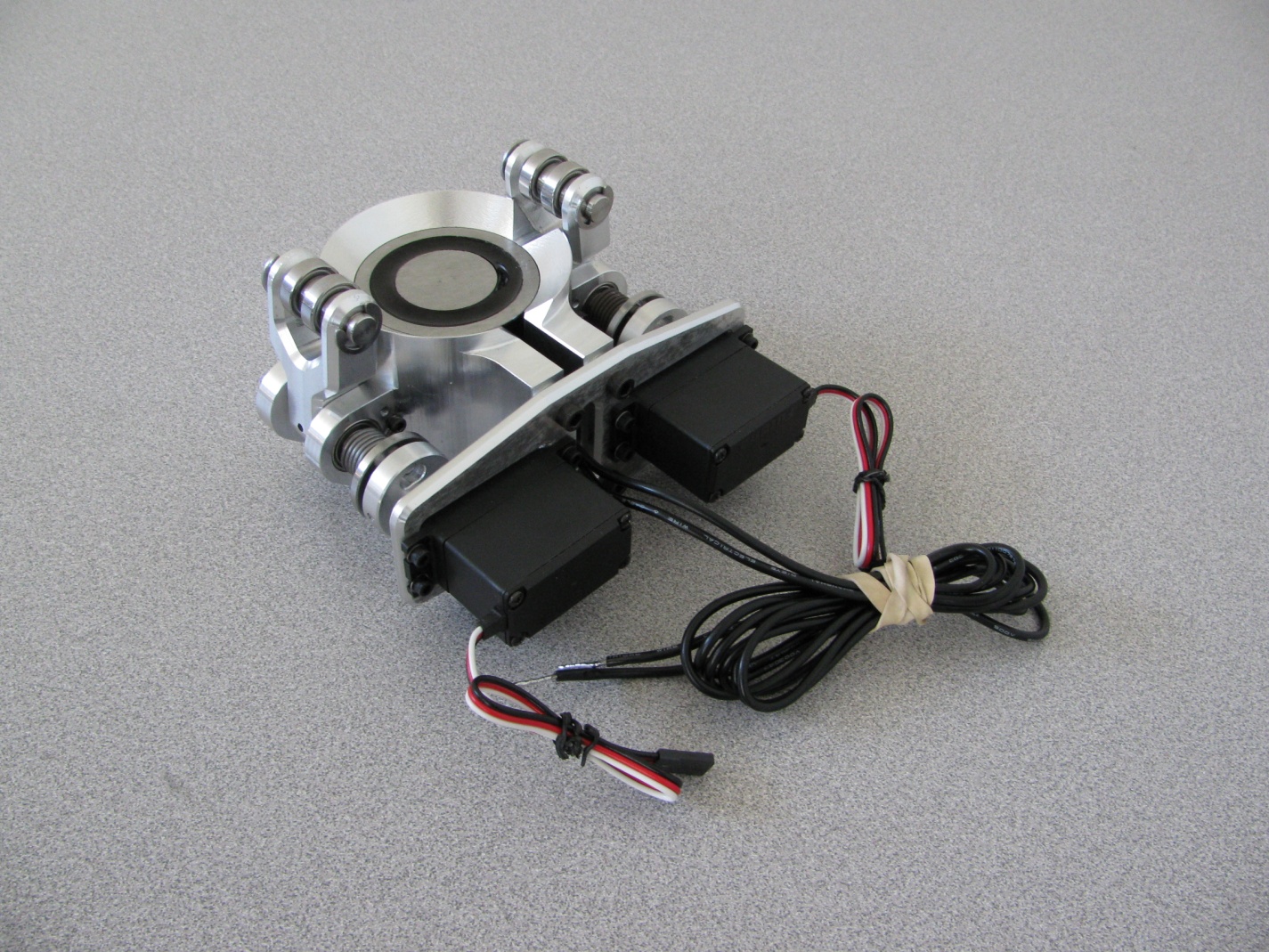
Electromagnet / Mechanical Plug Hard Dock
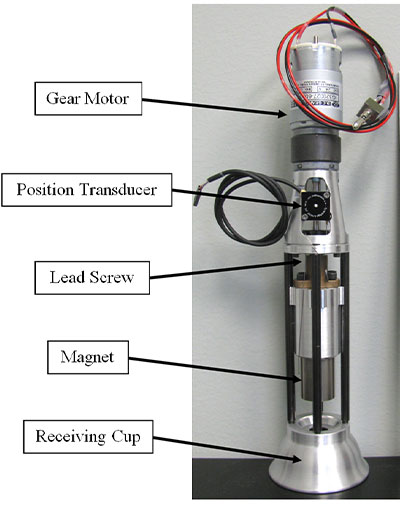
Permanent Magnet (Ball and Socket/Plug) Soft/Hard Dock
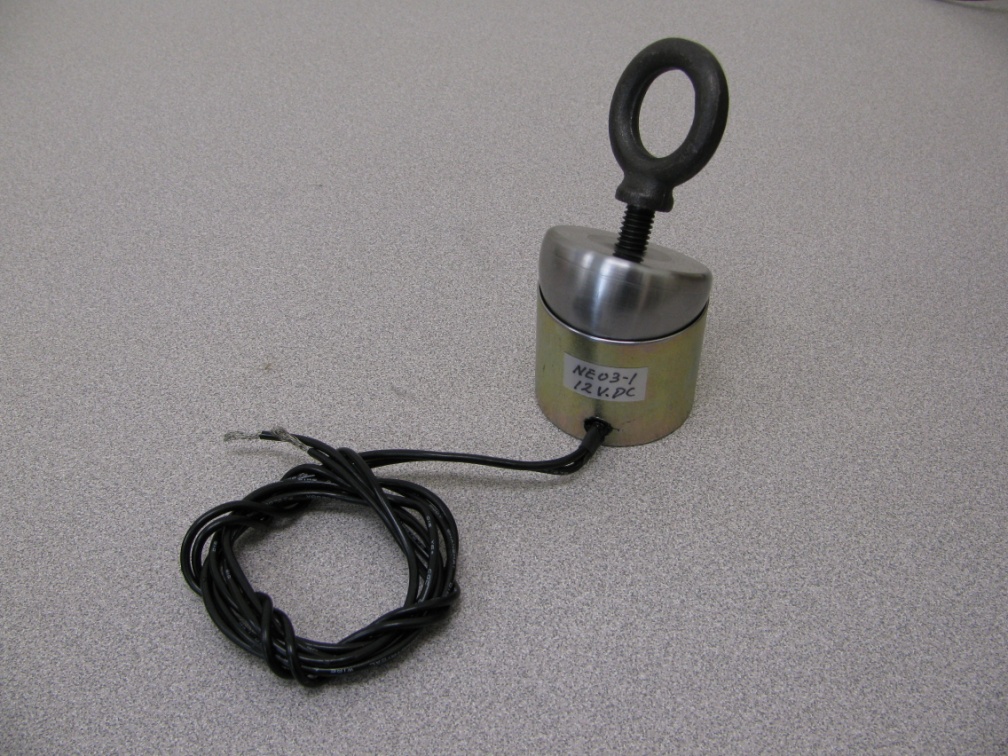
Electromagnet (Ball and Socket) Soft/Hard Dock
Progression of Flight Test Vehicles
Vehicles | Size and Uses | |
Sailplanes | Span: Weight: Tests: | 21.5 ft 57 lbs Risk reduction, AP piggyback |
Docking Vehicle | Span: Weight: Tests: | 14 ft 120 lbs Docking demonstration |
Sub-scale Cellular (33%) | Span: Weight: Tests: | 22 ft 187 lbs Subsystems, High/Low level controls |
Full-scale Cellular | Span: Weight: Tests: | 66 ft 900 lbs High altitude, Energy management |
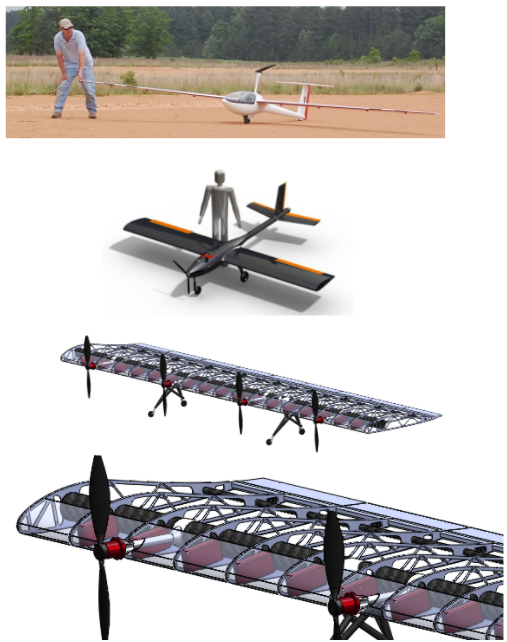
Goals for the Cognitive UAV Program
During the next two years NextGen will demonstrate key technologies in the Cognitive UAV program:
- Be the first to successfully demonstrate autonomous in-flight tip-to-tip docking of the cellular UAVs
- Complete design and manufacture subscale versions of the Cognitive UAV cellular aircraft
- Develop custom in-house cognitive control system capable of coordinating a group of cellular UAVs and docking tip-to-tip in flight